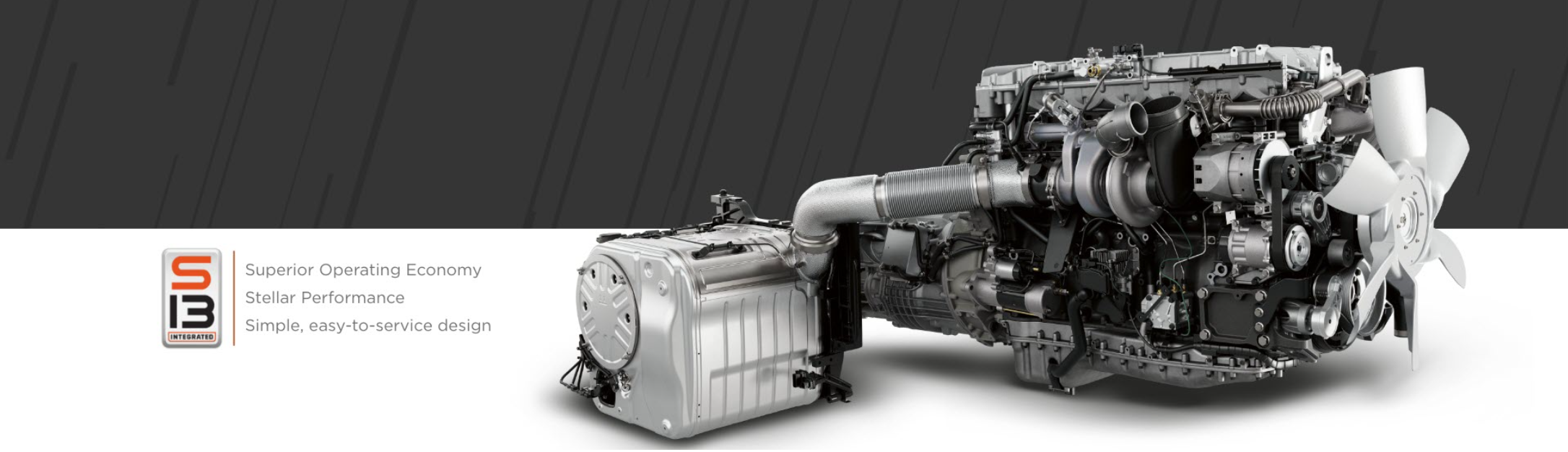
S13 Integrated Dual-Stage Aftertreatment System
The International® S13 Integrated Powertrain
Designed to allow each individual component – engine, transmission, and after-treatment – to focus on doing what it does best. Eliminating the EGR cooler is a prime example. Instead of trying to control NOx emissions inside the cylinder, the engine operates with zero-cooled EGR during regular operation, so it can focus on generating more power.
Plus, no EGR during normal operations means 100% of the exhaust flow goes through the turbo allowing the use of a simple, more reliable fixed vane turbocharger.
But no EGR meant our engineers had to find another way to treat NOx. They accomplished this by developing a next-generation Dual Stage Aftertreatment design that injects a first dose of DEF just downstream of the turbo in the evaporator tube and a second dose inside the after-treatment device.
And because much less soot (particulate matter) is generated, the engine does not need a diesel oxidation catalyst (DOC) and drivers no longer need to stop and perform the inconvenient task of active regens. The Dual Stage Aftertreatment system provides a simple, reliable solution that’s easily serviceable.
Delivering superior operating economy.
Through exhaustive simulation work, a new cylinder and piston head design with maximum cooling properties was created. This new double overhead cam design directly equates to less fuel being consumed. But that’s not all. Thanks to the new Dual Stage Aftertreatment system, the heavy (40-50 lbs), expensive ($2,500 approx.), and finicky EGR cooler is no longer needed to reduce emissions. Its absence not only contributes to the S13 being the lightest 13-liter diesel engine available in North America, but it also means 100% of the exhaust flow goes through the new simple, more reliable fixed-vane turbocharger for maximum performance and efficiency
Delivering the goods.
The S13 Engine can operate at low RPMs with high torque which equates to less fuel consumed while still delivering up to 515 horsepower and 1,850 lb-ft of torque. This incredible engine brings undisputed economy through combustion efficiency, the reduction of friction and pumping losses, and through use of new integrated software and controls.
MAKING THE SHIFT
The all-new, fully automated T14 manual transmission was designed in-house from the ground up. It’s a 14-speed overdrive transmission that is optimized to deliver peak fuel economy performance in direct drive (13th gear) during typical load. The transmission has an electronically controlled clutch actuator that works in sync with the engine to deliver faster, smoother shift performance. Since it does not consume air during complicated maneuvers like when you’re backing a trailer into a tight loading dock the driver never needs to stop and let the air recharge. The T14 also uses an integrated oil-to-water coolant system to optimize temperature regulation in both hot and cold environments. This advanced feature is one reason why the T14 is able to achieve an unlimited Gross Combination Weight Rating (GCWR)
UPTIME ABOVE ALL ELSE
A design that is simple, elegant, and easy to service
The entire powertrain was designed to allow each individual component engine, transmission, and aftertreatment to focus on doing what it does best. Eliminating the EGR cooler is a prime example. Instead of trying to control NOx emissions inside the cylinder, the engine operates with zero EGR during regular operation, so it can focus on generating more power. Plus, no EGR during normal operations means 100% of the exhaust flow goes through the turbo allowing the use of a simple, more reliable fixed vane turbocharger.
NEXT-GEN AFTER TREATMENT
Because there’s no EGR during regular operation, NOx must be treated a different way. To do this, the engineers developed an all-new Dual Stage Aftertreatment design that injects a first dose of DEF just downstream of the turbo in the evaporator tube and a second dose inside the aftertreatment container. Since a cooled EGR has been eliminated from the combustion chamber, much less soot or particulate matter is generated. This allows for extended service intervals and eliminates the need for active regens. In fact, the cleaner combustion cycle has so much less soot the engineers were able to eliminate the need for a diesel oxidation catalyst (DOC) in the after-treatment system. Combined, the after-treatment system provides a simple, reliable solution that’s easily serviceable.